Mother of Pearl Inlay, Abalone Inlay: 7 Creative examples.
The full beauty of our shell components is often revealed when combined with other materials, including solid timber and other favorites for artisans and interior decorators. This month, we take you behind the scenes and reveal some of the methods used for inlay.
Inlaying The Whole Shell
A simple idea, yet incredibly popular.
The groove can be carved manually with a chisel, but it is challenging to match the exact shape of the shell, hence very time consuming .
With the CNC machine, an initial 3D template must be created, then the shells are chosen to match the standard groove, as close as possible. For some shells, additional sanding on the outside will help for a better fit. A 2 parts epoxy glue is a handy filler for the little space left between the shell and the groove.
A final sanding is required to make the shell's edge flush with the board. A gloss coating will add the final touch, It includes the shell's inside, so it can be used for your dips. For cheese boards, New Zealand Abalone Paua is the obvious choice, thanks to it's outstanding color and concave shape.
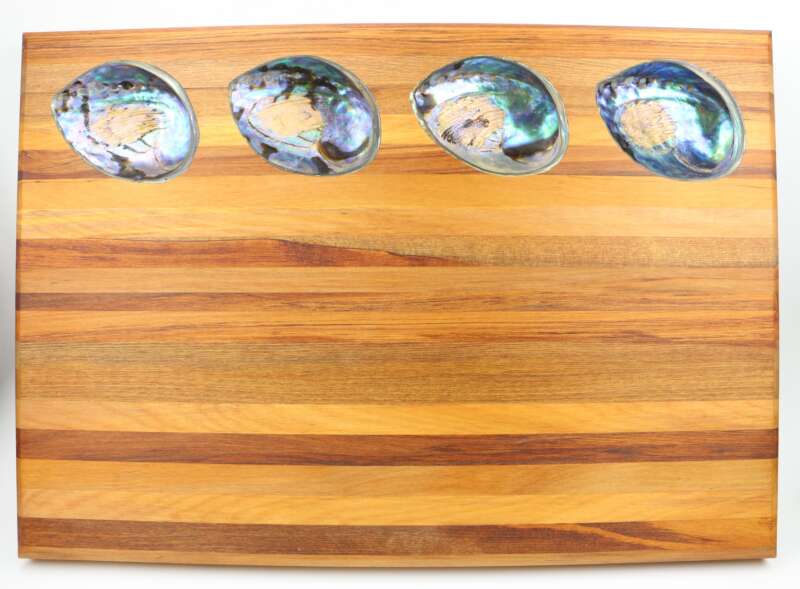
Shell Pieces For Inlay
A great way to add texture and a 3 dimensional feel to your inlay project, satin tumbled shell pieces add a point of difference that can feature in wall art and craft items. Here, we see the use of a good range of shells , including Abalone Paua, Black Mother of Pearl, and Pink Mussel.
This has been particularly successful when featured on our "Recycled Wood" items.
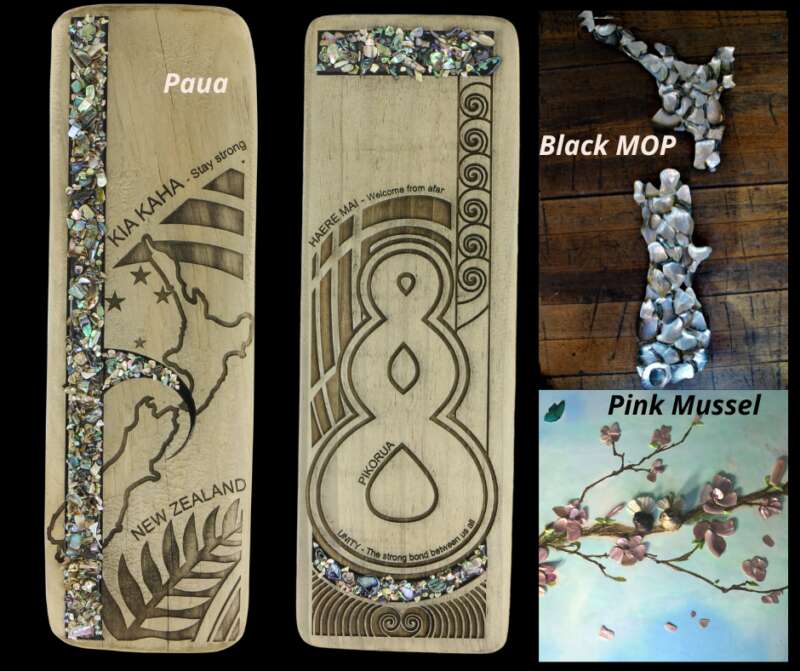
The inlay method is simple, and the result always appreciated! the groove only needs to be deep enough for the shell pieces to stick out.
Shell Veneer Inlay
We spoke about the manufacturing of Mother of Pearl Inlay Sheets in a previous blog. Inlay sheets are the most versatile semi-processed item from shells, because they come as a 0.25 mm thick sheet and can easily be inserted into a matching groove. You can either use some of the standard, non corrosive glues or simply rely on a double sided sticky tape material, with durable results.
Some of our clients have done inlays by carving the groove manually and also cutting the veneers by hand. The art of Mother of Pearl inlay (Najeon) started in Korea around the 16th century, when only hand made pieces were inlaid in perfectly matching recesses, hand carved from hard timbers.
Today, CNC machines deliver precise grooves and laser machines produce intricate shapes from veneers, ready to inlay in a matter of minutes.
Mother of Pearl Sheet, Precast in Resin Panel
When the inlay piece is intended for a sharply convex on concave piece. A thick resin casting, 4mm to 6mm, can be added to the shell sheet. The surface is then sanded or "turned" for a smooth transition between the wood and the inlay. A final gloss coating enhances the magnified look of the shell sheet through the resin layer.
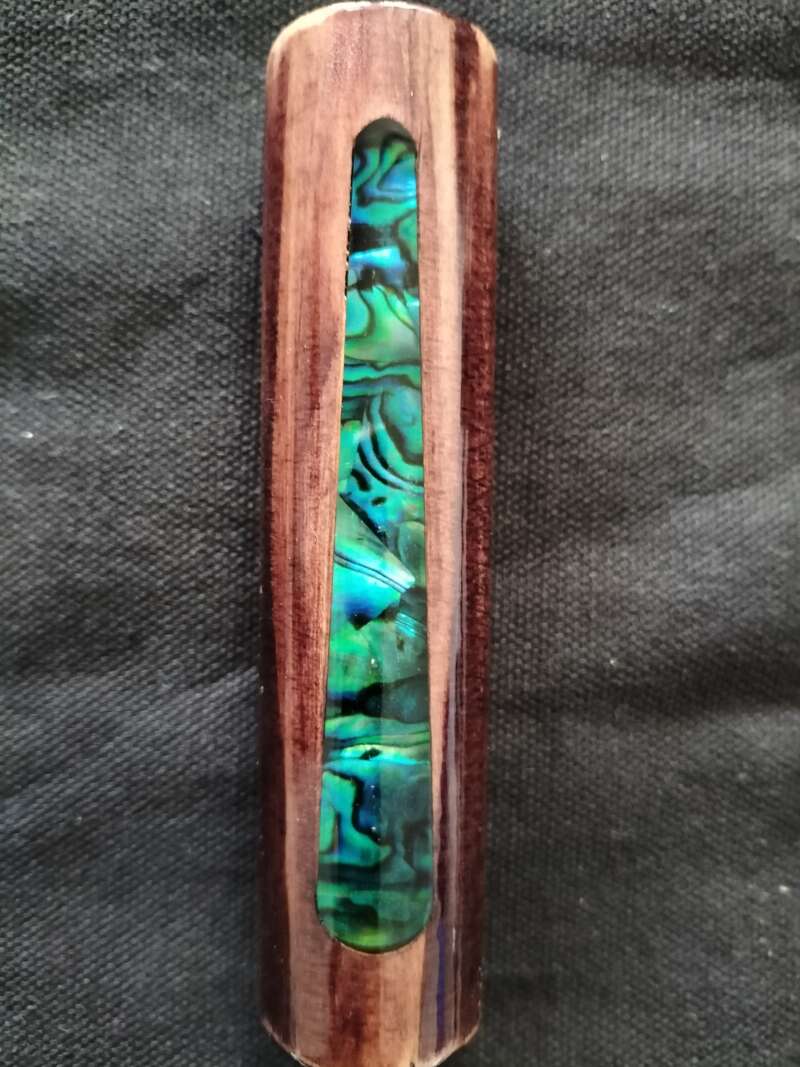
The method id used for pool cues, but can be adapted for inlay into pens as well.
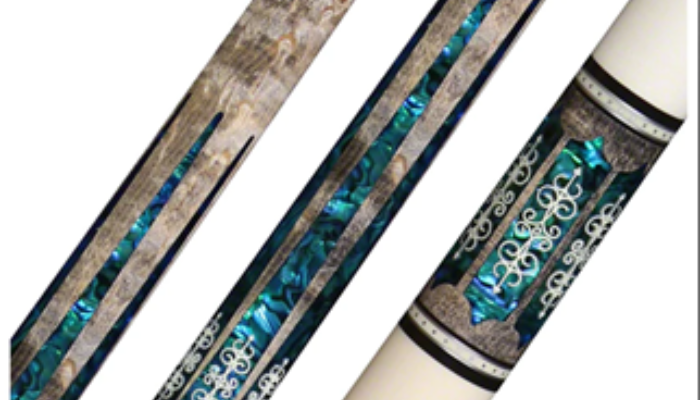
Wrapping The Shell Inlay Sheet, Using Heat.
Fishing rod, lures and pen makers have something in common. They need to get the maximum flexibility out of the mother of pearl sheet, to wrap it into a cylinder shape. Mostly it requires applying heat to the sheet, as per the video below. the process still tends to inflict some micro cracks to the material, but they are masked by the resin casting or the gloss coating on top.
For fishing lures the resin casting can be quite thick, but every lure maker has their own secret method. Here some lures from Eric Bouteille, Noumea.
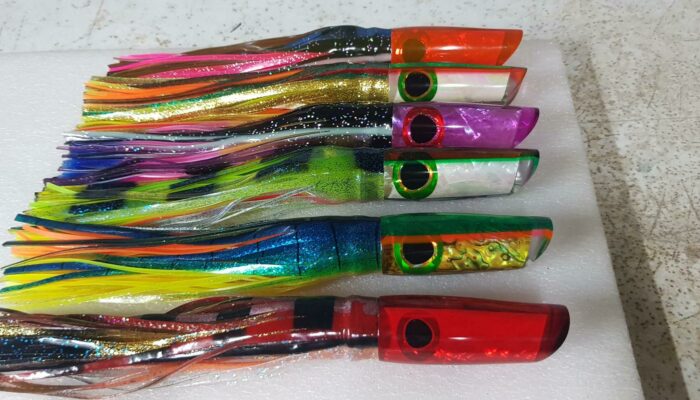
With the Fiordland Souvenir Pens, the Paua veneer is wrapped in a spiral shape, then resin coated: unusual, but successful!
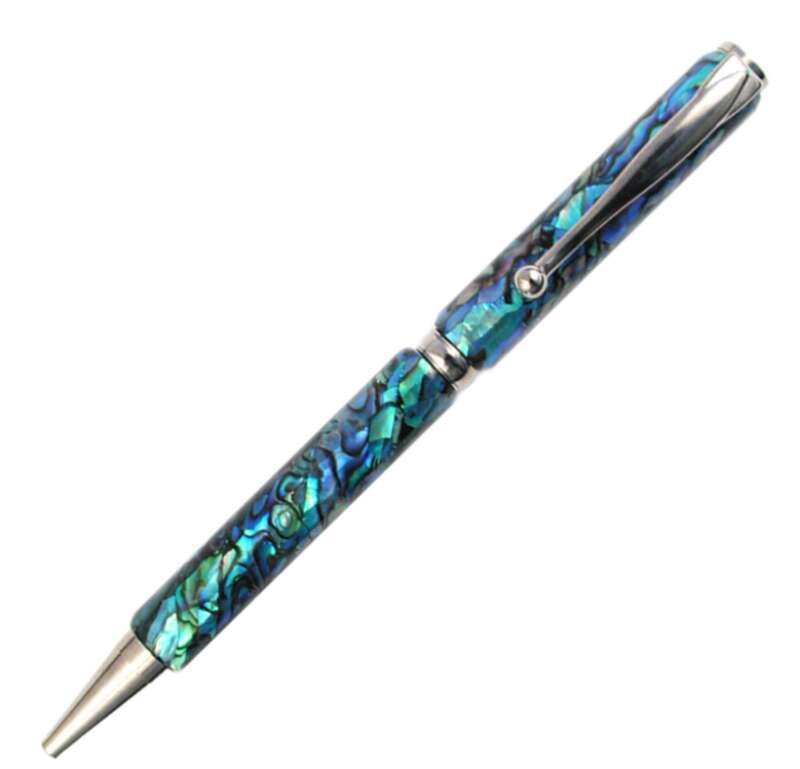
Shell Inlay For Silver Jewelry Casing
Laser cutting allows creativity and diversity once again. With a precise real size drawing of the shape you intend to fill with mother of Pearl or Paua, you can create the perfectly matching cut from the veneer sheet. The same flexibility was never possible when carving shapes directly from shells. The depth of iridescence in a very thin shell veneer sheet matches the effect of a polished shell fragment.
Shell Composite Inlay, a Thicker Material That Can be Sanded Down.
Mainly used by guitar and furniture manufacturers, composites are made of 3 or 5 Shell veneer sheets, as described in this dedicated blog post.
The thickness of composites means you can preserve the feel of solid shell, in a flat sheet. Because it is uncoated, the composite sheet can be gloss coated after being sanded flush with the wooden shape. It is ideal for slightly convex fretboards. Many furniture makers prefer the composite, as they do their own fine sanding, and final varnishing for a seamless result.
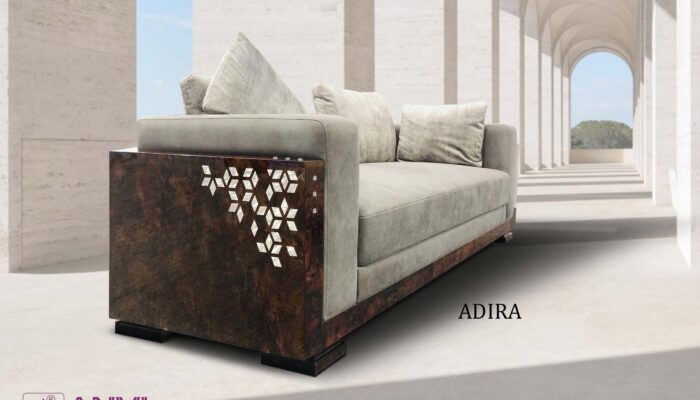
The Wild Card: Flexible Shell Veneer
To get the required flexibility, and allow full wrapping around a pool cue, a ball-pen, a fishing rod or fishing lure, uncoated flexible veneers are the answer. Manufactured by using just one very thin slice of shell (0.1mm or less) and inflicting microscopic cracks to the shell, this material can be combined with a great variety of supporting surfaces, including canvas and fabrics, a favorite for interior decorators.
Used here in a fit-out for a luxury brand store in Paris: Chanel.
Tell us about your project...
Your project is unique, so we provide personalised advice before delivering worldwide from our studio in New Zealand.
Luméa products are made from natural shell with a variety of factors that affect form and function. If you can’t find the right product from within our range, then talk to us about our custom design service. We love to experiment and collaborate with our partners to create unique solutions.